The demand and development of global wind power energy have significantly increased in the past decades. The wind power could be captured and converted into electricity through the wind turbine.
6
5
10
Hydrodynamic Performance Optimization of Trimaran Vessels for Offshore Wind O&M
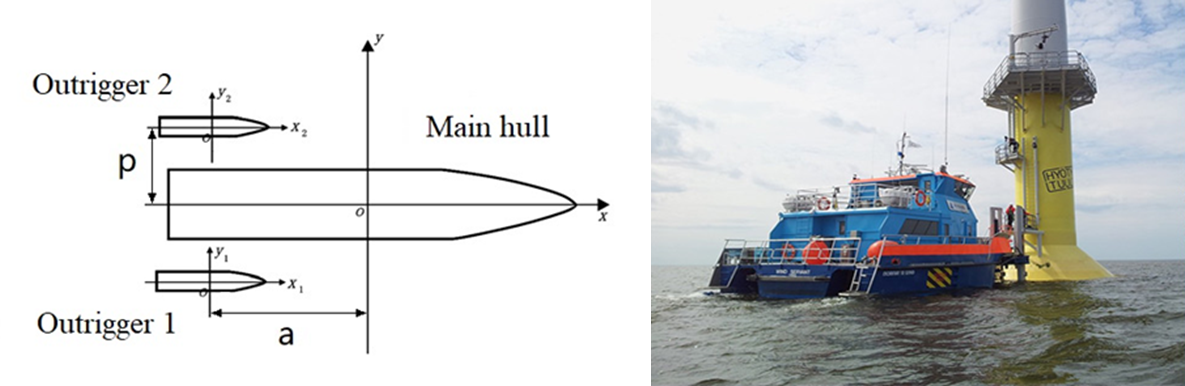
Wind energy as a clean renewable energy has attracted a lot of attention in recent years. The offshore wind power industry is also in a stage of rapid growth and development. During the operation of offshore wind turbines, regular maintenance is required, which relies on wind farm operations and maintenance (O&M) vessels to carry out these tasks. Trimarans, as high-performance vessels, offer advantages such as low wave-making resistance, excellent seakeeping performance, and spacious deck areas, making them well-suited for use as offshore wind O&M vessels to carry out maintenance tasks for wind turbines.
This project focuses on the hydrodynamic performance optimization of trimaran O&M vessels used for offshore wind. The primary goal of this project is to develop an efficient and accurate methodology for optimizing outrigger layouts to enhance the trimaran's overall hydrodynamic performance under specific sea conditions. The research includes several core components: first, an efficient hydrodynamic solver based on the Harmonic Polynomial Cell (HPC) method is developed to predict vessel motions with reduced computational cost. Building upon this solver, a multi-objective optimization framework is constructed using the Non-dominated Sorting Genetic Algorithm II (NSGA-II), which balances multiple performance objectives such as resistance, heave, roll, and pitch responses. To further accelerate the optimization process, a neural network is introduced which is trained by the existed data derived through numerical simulations during the optimization process.
Postdoc Shangming Wang and Professor Muk Chen Ong are the contact persons from UiS. The project started 1 Oct 2024, 30 months in total.
LOWT – Large Offshore Wind Turbines (LOWT)
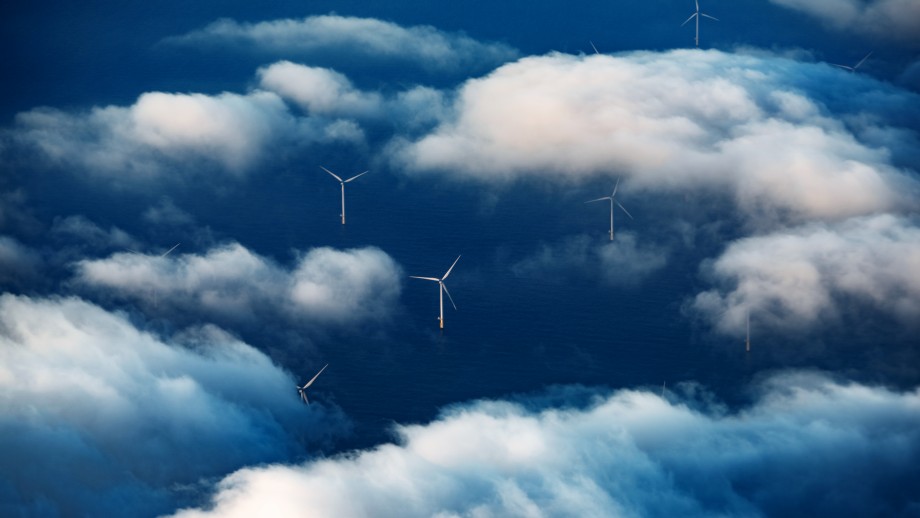
This project will develop new knowledge and models to improve the design basis for large floating wind turbines (LOWT)(>12MW) in freewind and wake conditions. Observations from Hywind Scotland have shown the thermal stratification of the atmosphere can substantially affect the structural response of a wind turbine to the incoming turbulent flow. The first objective is to use wind data from several offshore sites to characterise the wind field in non-neutral atmospheric conditions.
The project will use high-frequency wind data combined with a brand new remote sensing dataset (COTUR). In the COTUR campaign the incoming flow over the ocean was recorded, both within and above the surface layer, thus providing new insight on the applicability surface-layer scaling to model the turbulent wind loads on LOWT. This unique dataset will be analysed for the first time to the to indicate whether the turbulence models used in the standards, which mainly relies on surfacelayer scaling, are appropriate or not. The final output will be to recommend suitable wind and coherence model for in non-neutral conditions as input to free wind aeroelastic simulations and DWM models offshore. The second objective is to validate the simulated wind turbine response using full scale data from offshore wind farms (Alpha Ventus, Sheringham Shoal, and Zefyros/Hywind Demo). The validated simulation tools will then be used to quantify the effect of non-neutral atmospheric conditions on future LOWT (>12MW) to ensure safe and cost-effective design in the next generation of offshore wind farms in Norway and beyond. The final focus of the project is wake simulations of LOWT in non-neutral conditions using DWM model. High-fidelity CFD simulations will be used to include variable velocity shear in the DWM method and validate the wake meandering in non-neutral conditions. The non-neutral wind spectra and coherence from the data analysis work will be used as input for the DWM simulations.
The project is in collaboration with UiS, UiB & SINTEF. Project period is 2021-2025 and project leader is Charlotte Obhrai.
Former related projects include
- Derisk – De-risked extreme wave loads for offshore wind energy, a joint research project between the 9 partners: DTU Wind Energy, DTU Mechanical Engineering, DTU Compute, DHI, DONG Energy, University of Oxford, University of Stavanger, Statkraft and Statoil.
The project period is 2015-2019 and project leader is Charlotte Obhrai. - COTUR – COherence of TURbulence with lidars, remote sensing of offshore turbulence for wind energy application – UiB, NORCE, UiS, Equinor.
The project period is 2018-2020 and project leader is Charlotte Obhrai.
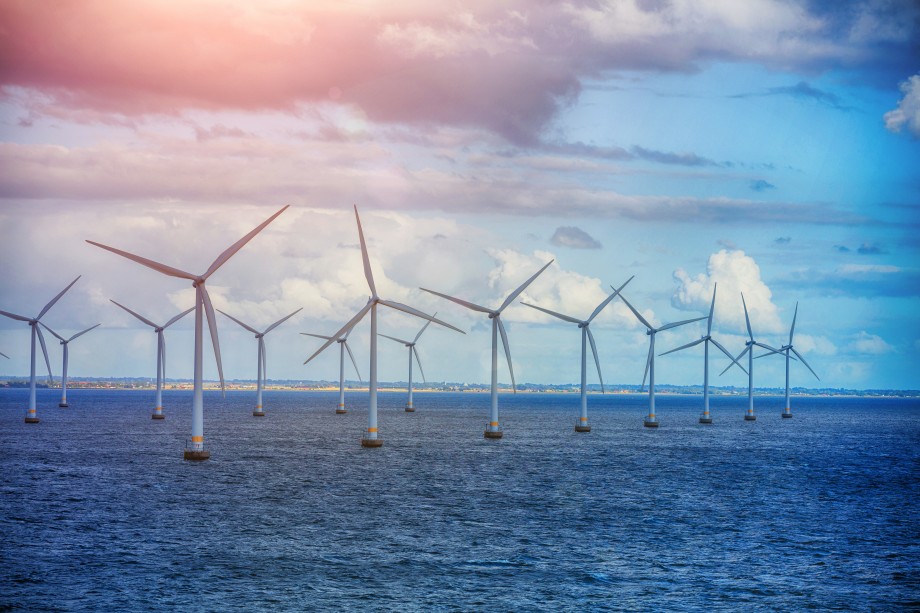
Floating offshore wind turbines
Wind turbines are mainly classified into horizontal axis wind turbines (HAWTs) and vertical axis wind turbines (VAWTs) in terms of the orientation of rotating axis.
As the aerodynamic efficiency of HAWTs is generally better than VAWTs, nowadays the application of HAWTs with higher commercial values are the mainstream in the world. Since larger wind resource and potential could be explored in deeper seas, wind farms are moving towards deep water in recent years.
Crucial dynamic responses
The floating offshore wind turbines have become the available solution which could be widely used in deep water. The spar, semi-submersible and tension-leg platform (TLP), which have been utilized in oil and gas industry for a long time, are three primary types of floating structures for offshore wind turbines.
The dynamic responses of these floating structures in the presence of the marine environment are crucial for a design purpose.
Prototypes
Several prototypes of floating HAWTs are developed, such as a catenary moored spar of the Hywind project in Norway, a semi-submersible of the WindFloat demo in Portugal, and a spar-type floating wind turbine of MOE project at Kabashima in Japan.
The commercial floating wind farm, i.e., the Hywind Scotland by Equinor, started its production in 2017.
UiS researchers have performed dynamic analysis of both semi-submersible floating HAWTs and VAWTs as well as spar-type VAWTs. Currently, UiS researchers are working on the dynamic responses of a spar-type VAWT integrated several wave-energy converters.
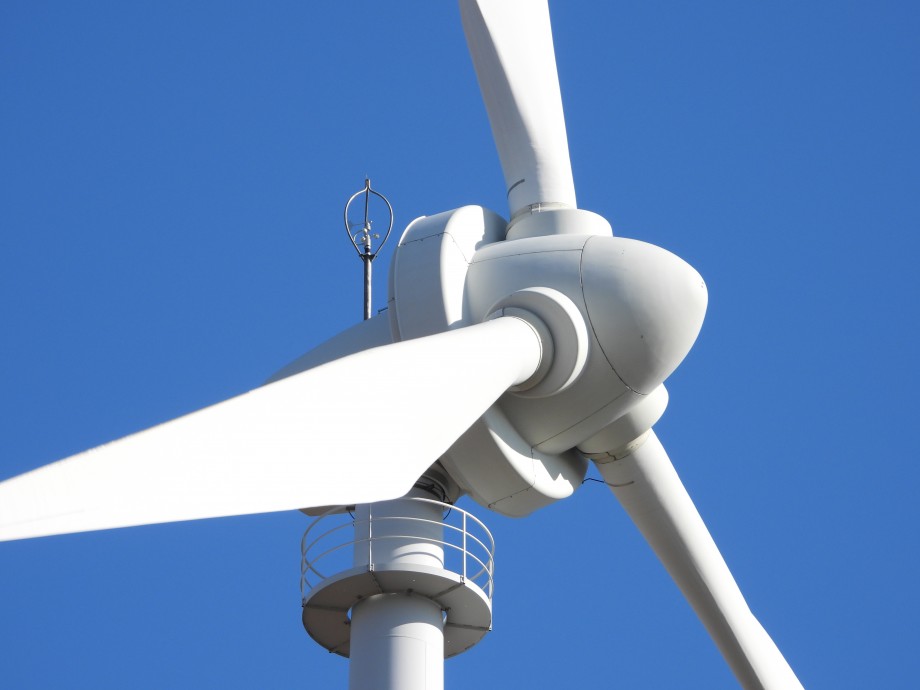
Aerodynamic Loads on Large Wind Turbines
Increasing wind turbine size combined with necessary design improvements is the prevailing approach to reduce cost of the wind power production.
Large rotor blades (e.g., 178 m and 252 m rotor diameter for a 10 MW and a 20 MW turbine respectively) will operate higher up in the marine atmospheric boundary layer (MABL) compared to the wind farms currently in operation, and often protrude above the so-called surface layer.
Full-scale measurements
The impact of such complex wind conditions for the design of wind turbines will be addresses by performing the full-scale wind measurements, as well as the advanced numerical simulations.
The offshore wind field at a site in the North Sea will be surveyed by optic wind sensors (so-called lidars), in collaboration with the University of Bergen (UiB), Christian Mikkelsen Research (CMR) and Equinor.
The activity will build on the pioneering work performed by UiS, UiB and CMR in 2014. The focus will be on capturing the spatio- temporal structure of turbulence, in particular the decreasing synchronization of the wind velocity fluctuations for increasing lateral distances in the rotor plane and increasing frequencies.
Computational analyses
The impact of the variable spatial structure of the wind velocity field on the fatigue and the extreme loading of relevant wind turbine designs will be studied by numerically simulating the representative wind fields and performing the related structural response analyses in time-domain.
Such analyses are computationally demanding, as they require a multi-body modeling of the wind turbine and its moving rotor, immersed in a simulated three-dimensional wind (and wave) field, and the response computations for a number of time-steps. This response analyses will be performed in collaboration with Statkraft.
Another relevant topic is the effect of wave-wind interaction on the aerodynamic loads and the power production. This will be studied utilizing the relevant full-scale measurement data, as well as performing the CFD simulations.
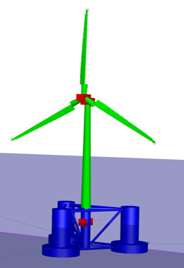
Numerical Scour Prediction Model for Offshore Wind Turbine Foundations
Many offshore sites for wind farms are located on seabeds of mobile sediments. For such cases, the interaction of the sediments with the turbine support structure must be taken into consideration.
Scour is the erosion of sediment in the vicinity of a structure, leading to a lowering of the seabed surrounding the structure. This can potentially be detrimental to the stability of the structure and its fatigue life.
Offshore turbine foundations are subject to high Reynolds number seabed boundary layer flows, which are induced by current and waves. To date, very few numerical studies have been performed to predict high Reynolds number flows around wind turbine substructures due to the complexity of the flow and the high demand on computational resource.
Currently, UiS professors and PhD students are developing a scour prediction CFD model.
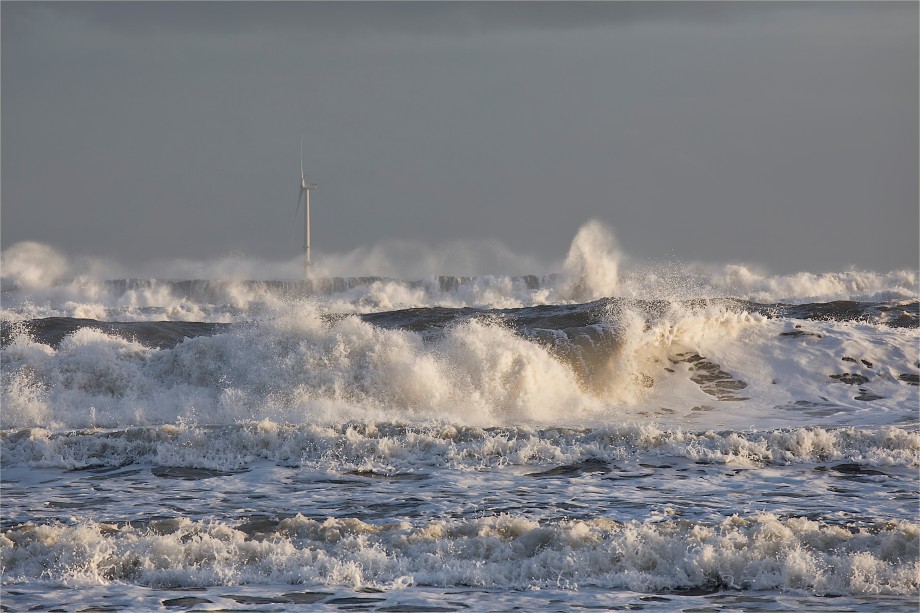
Modeling of Violent Breaking Wave Loads on Support Structures of Offshore Wind Turbines
Accurate prediction of breaking wave impact loads is a key factor in the design of maritime structures. The loading caused by steep storm waves impacting coastal and offshore structures has caused significant damage to vertical sea walls, caisson breakwaters, coastal bridges, oil platforms, FPSOs and LNG carriers.
Impulsive wave loadings are particularly difficult to predict, hence marine structures are often studied using hydraulic models and this generally introduces several ‘model’ and ‘scale’ effects. These combined effects result in deviation between loadings recorded in physical model tests and their real-world prototype equivalent hence in deviations between the up-scaled model and prototype observations.
A recent collaborative project between UiS and NTNU called WaveSlam aimed to investigate the wave slamming forces from plunging breaking waves on a truss structure in shallow water. A large-scale (1:8) jacket model was tested for plunging breaking waves in the Large Wave Facility in Germany. During the experiments, unique data sets were collected and recorded.
This valuable data set will be used to develop new load models for jacket structures and further validate CFD models developed in a previous PhD project for breaking wave loads on monopiles. A new study is also planned in cooperation with HR Wallingford in the UK to develop a compressible multiphase flow solver based on OpenFOAM capable of generating stable, coherent and statistically meaningful wave time histories of breaking wave loads on marine structures.
It is expected that results from this research will be used to shed light on the complex physics that stands behind wave-structure interaction, improve modeling capabilities and give recommendations to improve empirical formula for practical design purposes.

Installations of offshore wind turbines
The installation of offshore wind farms presents great challenges as the industry move farther offshore and into deeper waters, and the turbines and foundations are getting larger and heavier.
Current installation methods are all sensitive to weather conditions: lifting the foundations using floating crane vessels, deploying and retrieving jack-ups' legs, and lifting turbine nacelles and rotors at a large lift height. Careful studies on these critical installation scenarios during the planning phase of the installation are important.
The research at UiS (Professor Muk Chen Ong og Associate Professor Lin Li) focuses on numerical analysis of various marine operation and installation activities for offshore wind turbine foundations. An example is the use of numerical study on lifting operation for a tripod foundation. Complicated numerical models are established, and critical responses which limit the weather windows are analyzed.
The simulations serve as important input for planning and execution of marine operations. Furthermore, measures to increase operability for such weather-sensitive operations will be proposed, which may reduce the installation cost. This is an internal research project at UiS.
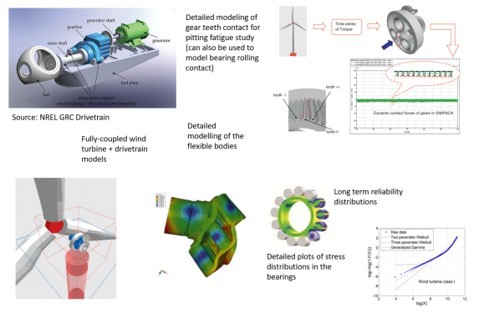
Offshore Wind Turbine Drivetrain Modelling
The offshore wind turbine is a complex machine that is subjected to tough offshore environmental conditions and access for maintenance, repair and overhaul is limited and expensive. It is therefore important to understand the offshore wind turbine drivetrain because gearbox failures have consistently plagued the wind energy industry and have not been able to reach the 20 year design life. Moreover, gearbox failures often result in massive downtime. Some industry players have even labelled the gearbox as the ’missing link’. There is a need for new insight into the understanding of drivetrain dynamics from an offshore perspective in order to improve its design and better predict its life. The findings in this thesis contribute to the de-risking process of offshore wind.
In this research, detailed models of the wind turbine drivetrain including its individual components are developed and analysed in detailed to reveal important drivetrain dynamics.
This is an ongoing project at UiS lead by Professor Yihan Xing.
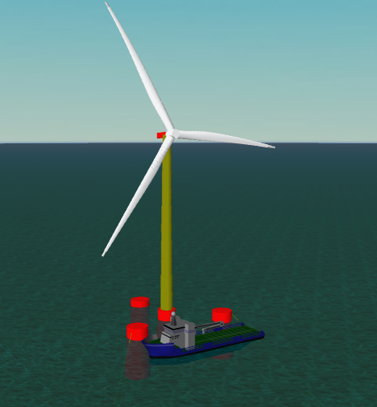
Ship impact with offshore wind turbines
An increasing number of floating offshore wind turbines (FWOTs) have been proposed and designed in recent years. FOWTs are under the threat of accidental collisions from supply vessels and passing ships.
Ship collision can induce local damage in the concrete or steel floaters which may further lead to flooding in these supporting components. Apart from local damage in the floater, the global response of the floating wind turbines under ship collisions can also be significant. The FOWTs may endure failure in the mooring lines or even the capsizing of the whole structure.
The UiS team is performting scaled experimental tests and numerical simulations to unveil the real behavior of FOWTs under accidental ship collisions. Both design optimizations and retrofitting techniques will be proposed to ensure the safety of FOWTs.
Researchers at UiS: Professor Jasna B Jakobsen and Associate Professor Yanyan Sha
ImpactWind SouthWest
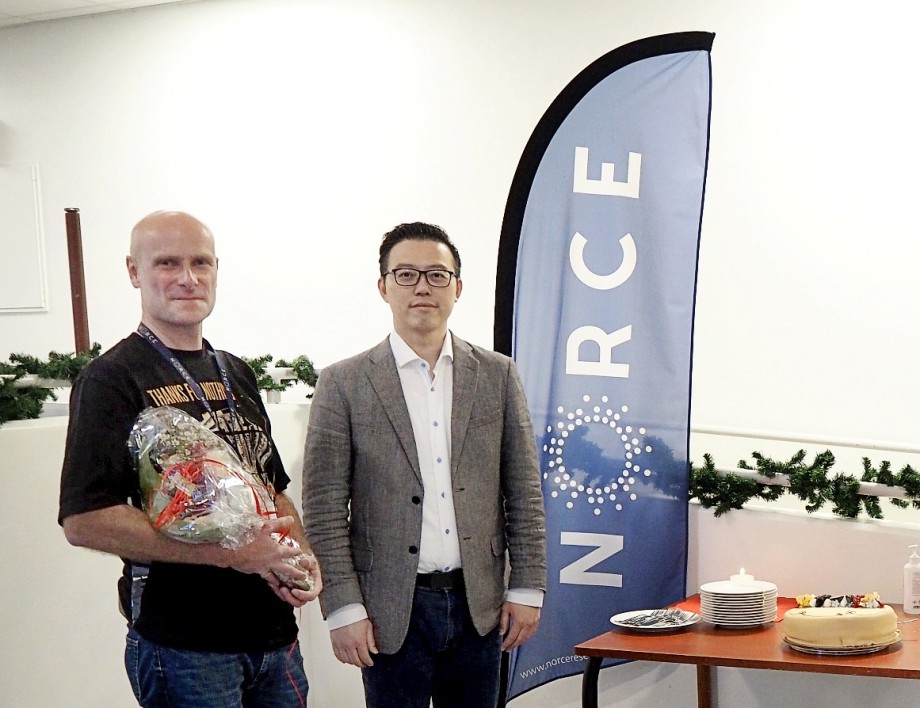
The growing offshore wind sector highlights overlapping interests in use of the marine area. The Norwegian government is therefore setting up a licensing process with pre-qualification before award of areas and then two years of thorough impact assessments before eventual awards of licenses to develop the areas. The impact assessment phase is complex, involving many different disciplines, and may, if poorly executed, be a "show-stopper" delaying the development phase and leading to challenges for investors and industry. To avoid unnecessary delays in the development of offshore wind, this project will provide better access to relevant data, more research-based knowledge, and dissemination of research-based knowledge through seminars and higher education.
ImpactWind Sørvest brings together 1 regional research institute, 3 regional universities, 4 business clusters, 2 national industry associations and 7 license applicants in an interdisciplinary capacity boost aimed at the license application processes.
Ten specific knowledge gaps have been identified based on dialogue with business clusters, industry associations and relevant industry partners, and the project consortium's professional knowledge: 1) Impacts on the marine environment. 2) Spatial competition. 3) Circular designs. 4) Cost efficiency and optimization of working conditions for personnel. 5) Social acceptance. 6) Employment development. 7) Climate impact on wind resources, micro-climate, and legal issues. 8) Climate consequences for development and operation. 9) Risk and consequences of accidents. 10) Standards for ongoing monitoring of the environment and facilities.
Professor Muk Chen Ong is work package leader for the project.
More information in the project web page.