UiS researchers study a range of issues connected to Offshore and Subsea Technology.
9
6
13
Sparse Measurement-Based Reduced-Order Models of Fluid-Structure-Interactions (SMARTFLUIDS)
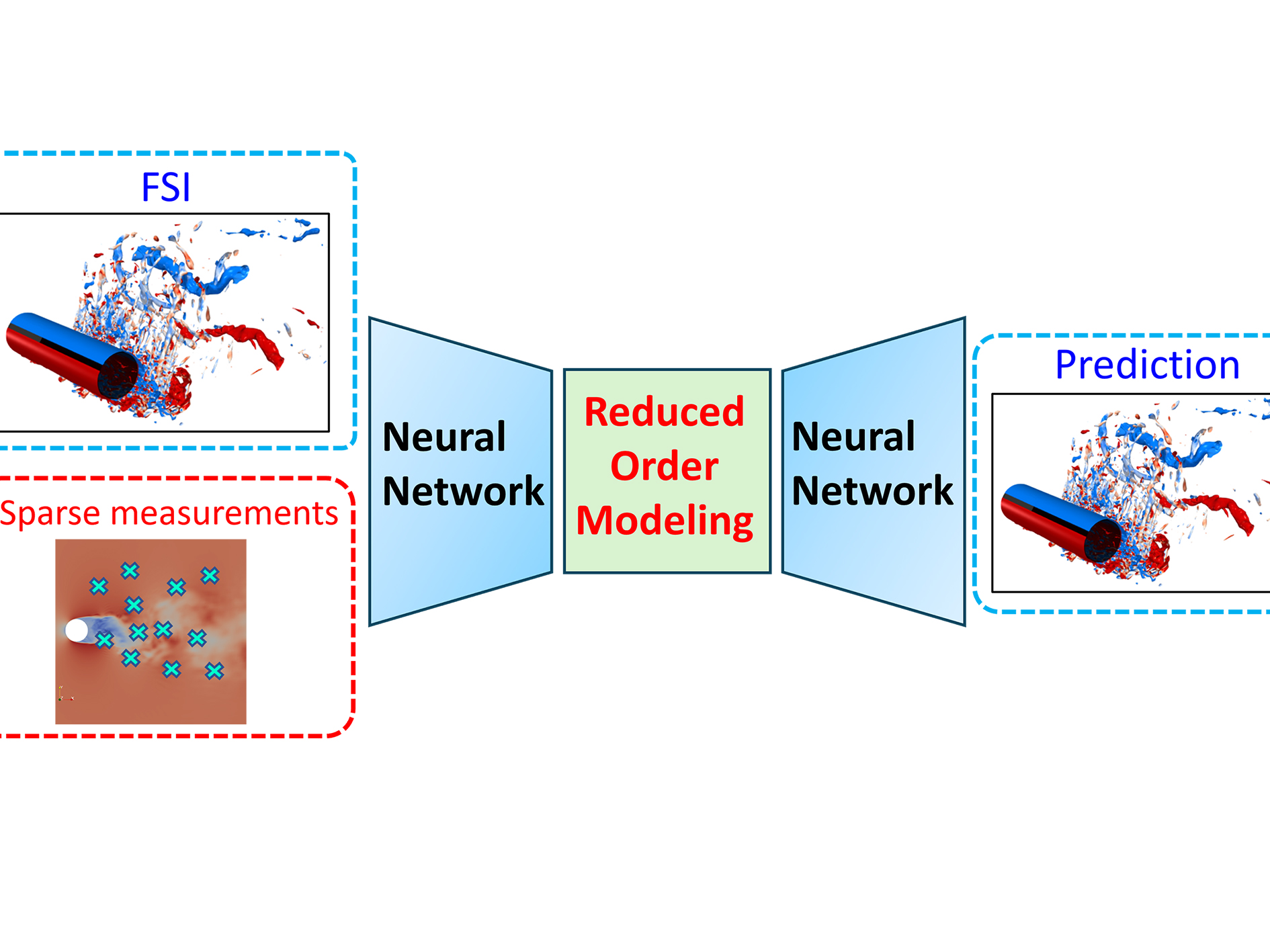
Fluid-structure interaction (FSI) plays a critical role in a wide range of industries—from ocean engineering and aerospace to biomedical applications and renewable energy systems. Accurately predicting the complex, nonlinear dynamics that arise from the interplay between fluids and structures—especially under turbulent conditions—remains a significant scientific and engineering challenge. This complexity often results in high computational costs and limits our ability to design efficient and robust systems.
SMARTFLUIDS addresses this challenge by developing an innovative framework for creating Reduced-Order Models (ROMs) that capture the essential physics of FSI with significantly reduced computational effort. The goal is to deliver low-complexity models that retain high fidelity in representing dominant physical mechanisms, enabling faster and more insightful predictions of FSI dynamics.
At the heart of the SMARTFLUIDS approach is the integration of deep learning with physics-informed modeling. A low-dimensional representation of FSI behavior will be learned using Variational Autoencoders (VAEs) trained on data generated from high-fidelity CFD simulations of benchmark FSI problems. Governing equations will be mapped onto this reduced subspace, where data-driven techniques will handle nonlinear and unresolved components. Physical constraints and sparse measurements will be strategically incorporated to ensure robustness and interpretability.
The resulting models will allow for efficient prediction of structural responses, hydrodynamic and aerodynamic forces, and future flow states—transforming how we approach engineering design in applications such as subsea pipelines, power cables, wind turbine blades, and aircraft wings. By significantly reducing the time and cost associated with traditional CFD and experimental methods, SMARTFLUIDS contributes to accelerating the development of clean and sustainable energy technologies.
SMARTFLUIDS combines cutting-edge machine learning with foundational fluid mechanics to offer an efficient and physics-informed approach to modeling FSI—paving the way for smarter, faster, and more resilient engineering solutions.
Dr. Guang Yin and Professor Muk Chen Ong are the contact persons from UiS. The project started 1 Jan 2025, 60 months in total.
Hydrodynamic Performance Optimization of Trimaran Vessels for Offshore Wind O&M
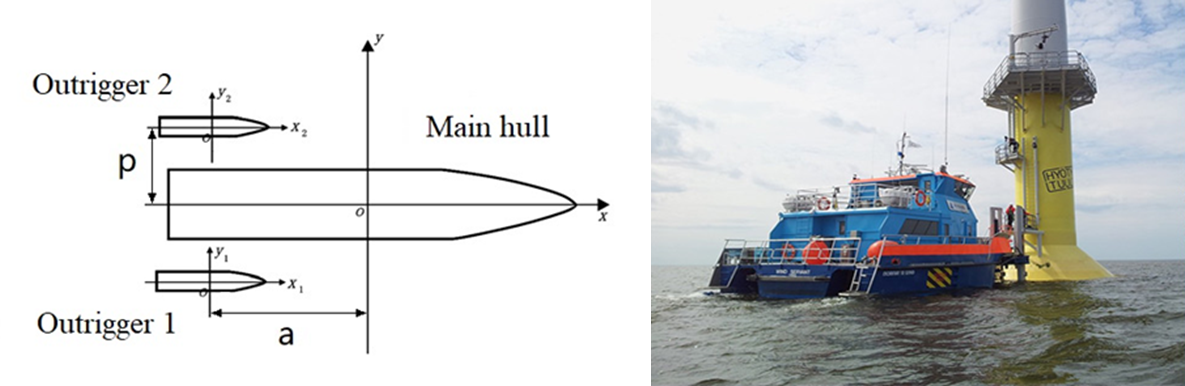
Wind energy as a clean renewable energy has attracted a lot of attention in recent years. The offshore wind power industry is also in a stage of rapid growth and development. During the operation of offshore wind turbines, regular maintenance is required, which relies on wind farm operations and maintenance (O&M) vessels to carry out these tasks. Trimarans, as high-performance vessels, offer advantages such as low wave-making resistance, excellent seakeeping performance, and spacious deck areas, making them well-suited for use as offshore wind O&M vessels to carry out maintenance tasks for wind turbines.
This project focuses on the hydrodynamic performance optimization of trimaran O&M vessels used for offshore wind. The primary goal of this project is to develop an efficient and accurate methodology for optimizing outrigger layouts to enhance the trimaran's overall hydrodynamic performance under specific sea conditions. The research includes several core components: first, an efficient hydrodynamic solver based on the Harmonic Polynomial Cell (HPC) method is developed to predict vessel motions with reduced computational cost. Building upon this solver, a multi-objective optimization framework is constructed using the Non-dominated Sorting Genetic Algorithm II (NSGA-II), which balances multiple performance objectives such as resistance, heave, roll, and pitch responses. To further accelerate the optimization process, a neural network is introduced which is trained by the existed data derived through numerical simulations during the optimization process.
Postdoc Shangming Wang and Professor Muk Chen Ong are the contact persons from UiS. The project started 1 Oct 2024, 30 months in total.
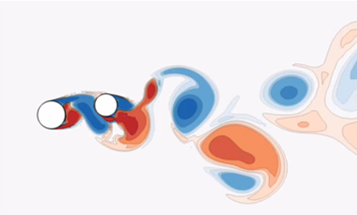
Fluid-Structure-Morphology-Soil Interaction CFD Model
With the rapid development of seabed oil industry, the technology of subsea systems draws substantial attention in offshore engineering. It also increases the importance of flow structure interactions around subsea structures (such as subsea manifolds, subsea protection covers and marine pipelines) in different environmental conditions.
In order to achieve good operational conditions and accuracy of the installation process, it is essential to assess hydrodynamic loads acting on subsea structures precisely. Moreover, in areas with soils that are prone to scouring by current and waves, the stability of the structures and associated with the protection will be affected.
The hydrodynamic responses and the flow pattern around the structures will be subsequently altered due to the existence of the scour hole; and it further leads to a change of soil strength beneath the subsea structures, which might cause additional soil displacement.
This research study (supported by UiS-Equinor Academic Program) focuses on developing a computationally-efficient fluid- structure-morphology-soil interaction model based on the understanding of the flow physics and soil mechanics. An open-source CFD code, OpenFOAM is used for the model development. The effects of seabed boundary layer flow on the structures are considered.
The effects of Reynolds number, different configurations of subsea structures, boundary layer thickness of the incident flow and different soil properties are investigated.
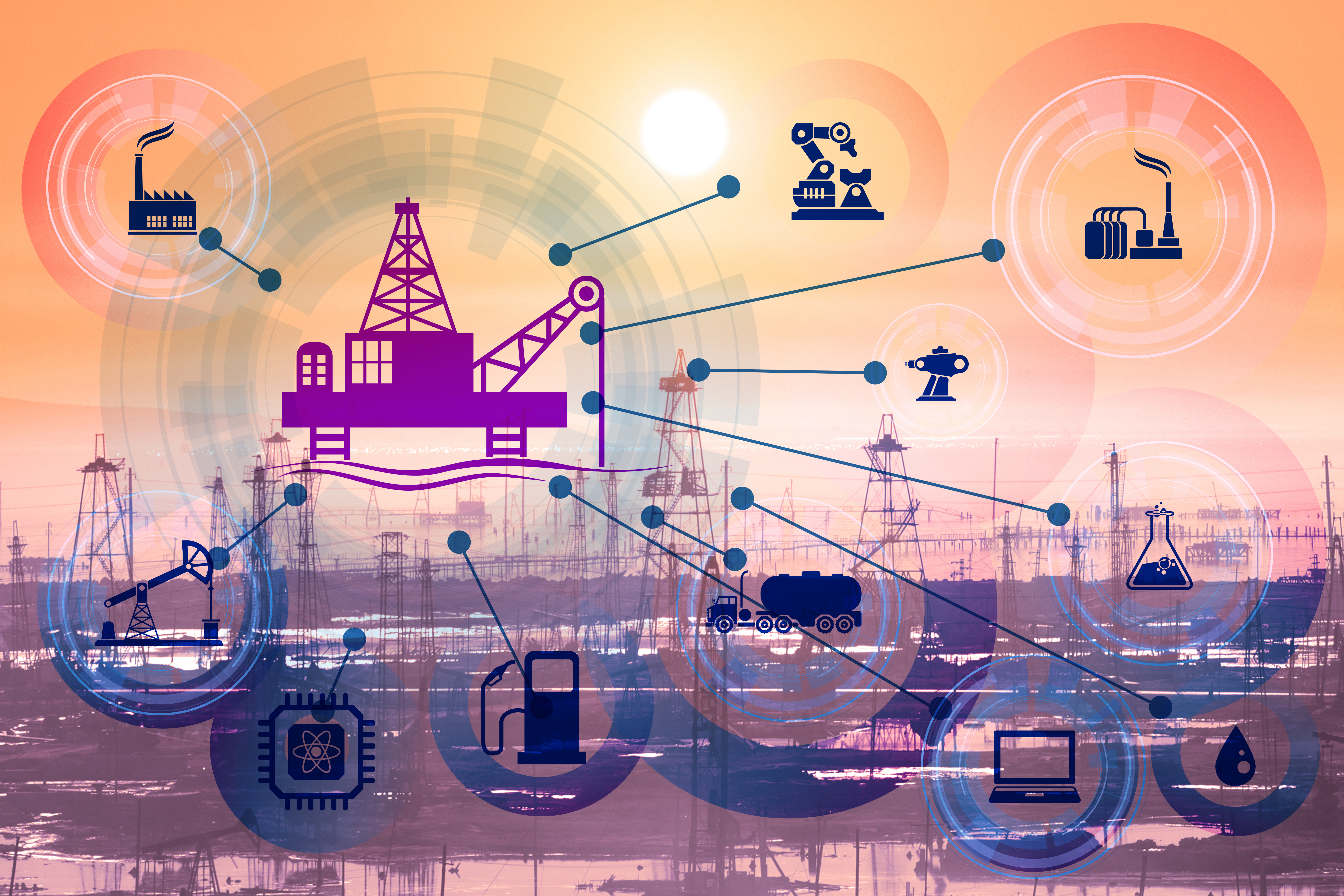
Drillbotics Project
In recent years, popular topics such as digitalization, machine learning, digital twin and big data have evolved from being envisions of the future to a fully integrated concept, expected to revolutionize drilling efficiency in the industry.
Drilling automation tomorrow is all about exploiting the current state of technologies available to the entire operation of drilling a well. Not only drilling automation can limit costs and reduce the risk to rig personnel and the environment, but also, they allow previously inaccessible oil resources to be developed.
There are, however, some challenges in keeping up with the ever-increasing pace of the development. Testing of novel and innovative solutions is often very expensive because of non-productive time during implementation, trial runs and data collection. In addition, the modern technologies require extensive prototyping and R&D before early testing can even commence, considering the potential extent of damage if an error should occur. Of great importance, the introduction of a state-of-the-art system can require significant upgrades across the entire platform and may thus only be partially implemented because limited data exist on the benefits of performing a full transition.
The research work at UiS is led by Professor Dan Sui is to test a laboratory-scale autonomous drilling rig to utilize fully interchangeable key drilling systems, sensors and tools that are all relatively inexpensive, little- to no risk of incidents involved, full-time access to the systems and immediate on-site results when testing prototypes or implementing models, algorithms etc.
By implementing the control architecture algorithms for real-time optimization of drilling parameters, the drilling rig can increase the performance efficiency and detect and handle incidents that would damage the system. The lessons identified can then be used to further strengthen the understanding of common causes of drilling incidents such as stuck pipe, key seating as well as drill bit wear. This study aims to develop better models that can be related to real-life drilling phenomena. The project started from 2017 and has been running for a long term period. The project is fully funded by the Science and Technology faculty and IEP department at UiS.
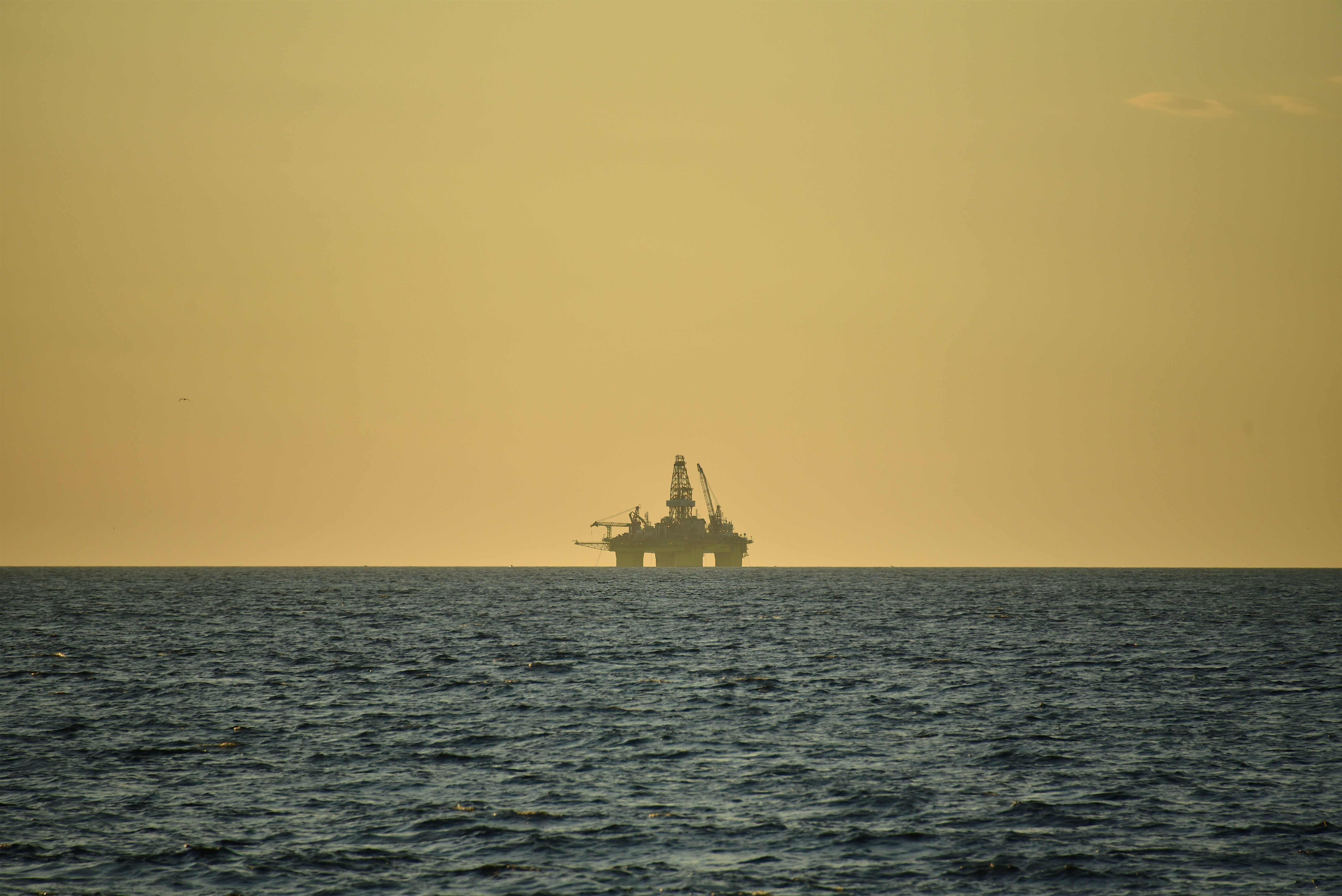
Deep-Sea Mining
With the advancement of offshore oil and gas exploration and production technologies, the mining activities in the oceans are no longer unattainable. The deep-sea mining industry has attracted growing attention globally as they target mining activities in deeper waters of up to 6,000 m depth. It is known that the Canadian company Nautilus Minerals is now developing a real deep-sea mining project in Papua New Guinea. Meanwhile in Europe, there are two European Union sponsored research projects, known as ‘Blue Mining’ and ‘Blue Nodules’ emphasizing on the ‘breakthrough solution for sustainable deep-sea mining’ and ‘to develop a new highly-automated and technologically sustainable deep sea mining system’.
Multi-disciplinary
The entire deep-sea mining system is highly integrated with multi-disciplinary technology and knowledge, including
- ship hydrodynamics
- ultra-deep water ship dynamic positioning
- riser flow-structure interaction
- riser internal multi-phase flow
- complex boundary conditions, including top motion compensation device and bottom flexible jumper connection.
It is known that many of the technologies used in the deep-sea mining have been adopted from the offshore oil and gas industry. However, one of the most significant challenges is to develop a thorough design and optimization package which is capable of considering all relevant dynamic behaviors in the entire deep-sea mining system.
System analysis
This research study focuses on developing a fully coupled global dynamic analysis package for the deep-sea mining system in the time-domain.
The proposed numerical investigation includes ship potential theory, control algorithm, slender structure finite element modelling, structural dynamics and their coupling effects. Inputs from computational fluid dynamics (CFD) calculation are implemented to accurately addressing the loads during fluid-structure interaction.
This research aims at increased understanding and improved design of the deep-sea mining system. This in an ongoing study by Professor Yihan Xing, Professor Muk Chen Ong and Professor Dan Sui.
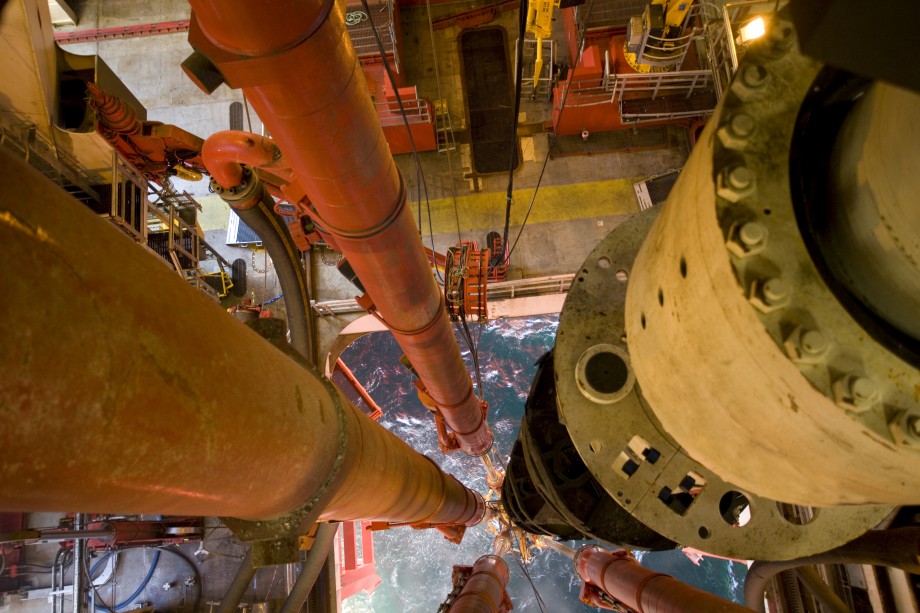
Demonstrating Safety of Novel Subsea Technologies
This project, funded by the Norwegian Research Council and several industry partners (2018-2021), is led by DNV and has both UiS and NTNU as academic partners.
The main objective of the project is to enable and accelerate up-take of novel subsea solutions by developing a framework for standardized demonstration of safety, including examples of common acceptable design solutions. The framework will be developed from relevant use-cases, and will support introduction of new safety philosophies, more integrated solutions, and advanced use of sensor data and data analytics, to demonstrate a sufficient level of safety.
Researchers at UiS are Professor Roger Flage, Adjunct Associate Professor Andreas Falck, Post Doc Christine Nyvik.
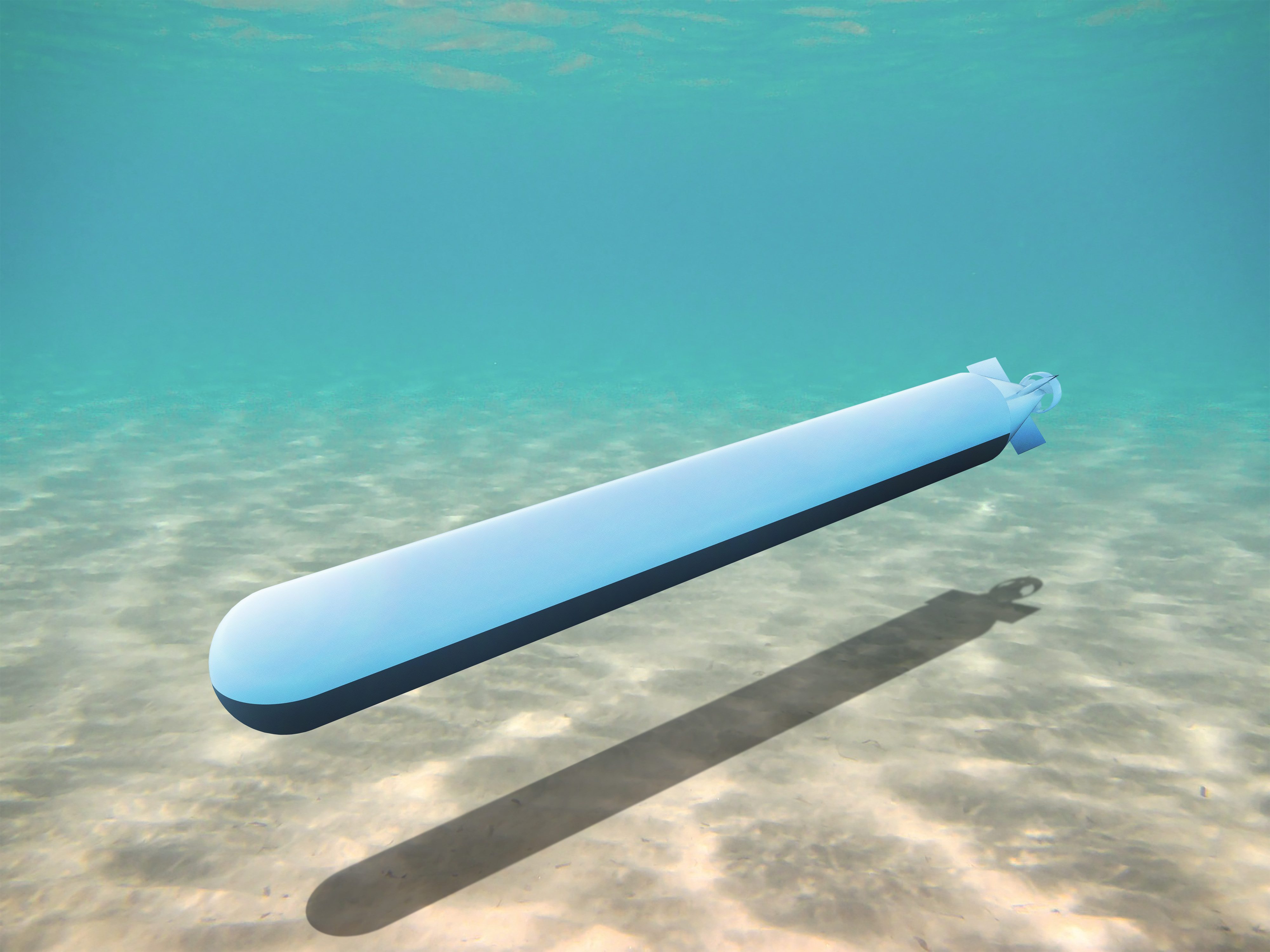
Autonomous Subsea Shuttle Tanker
Researchers at OTICS, Professor Yihan Xing, Professor Muk Chen Ong ang PhD student Yucong Ma are working on a novel autonomous subsea shuttle tanker to transport carbon dioxide liquid to marginal subsea fields on Norwegian continental shelf. This new concept has the potential to enable the exploitation of these fields as carbon storage sites, which would be otherwise economically unfeasible. In addition, the SST also seeks to minimize its carbon footprint by operating at a slow constant speed to reduce energy consumption.
The researchers have proposed a 32,000 tonnes baseline design in which a unique double-hull arrangement with active pressure compensation capabilities specially designed to handle deep water depths, allowing for a high load capacity to structural weight ratio. To establish a good understanding of the SST concept, in depth-research is conducted using this baseline design into key features and systems such as the dynamic behaviour analysis, control strategies, landing sequence and active pressure compensation system.
Additionally, scaled model tests are also planned to be carried out in the future. This is a three year project ending in July 2023.
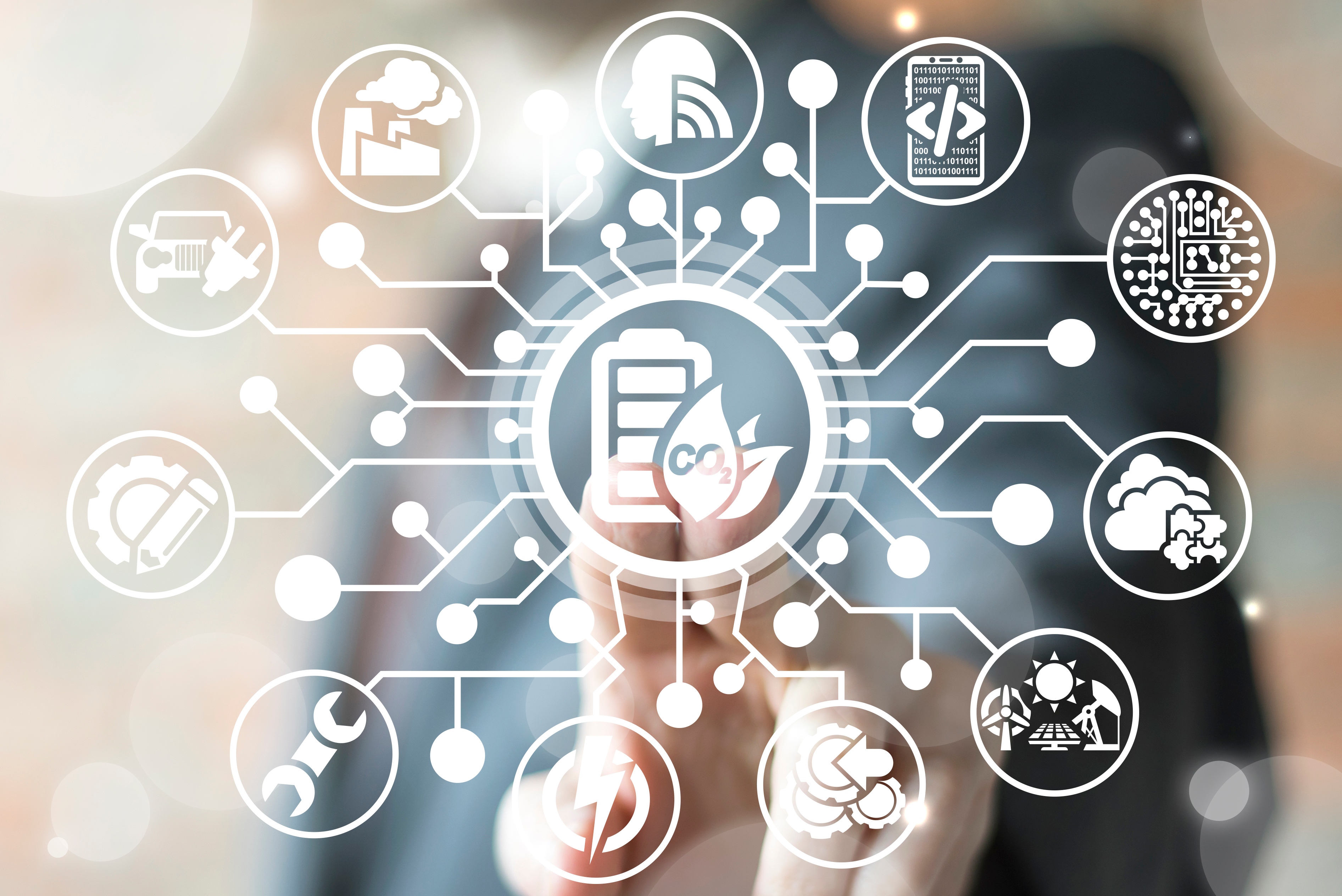
Horisont Energi AS - «Feasility study of a new CCS value chain»
CCS stands for Carbon Capture and Storage or “karbonfangst og lagring” in Norwegian. CO2 levels in the atmosphere are gradually rising. Profitable CO2 storage solutions are crucial in the combat against global warming and in the reduction of climate emissions. In this study, Horisont Energi AS in collaboration with the University of Stavanger analyzed, modelled and simulated critical and technical uncertainties in specific parts of a new CCS value chain. Based on the results obtained, a technical CCS solution that is realizable and operable on an industrial scale is identified.
Autonomous near surface geophysical acquisition with applications to underwater archeology and construction
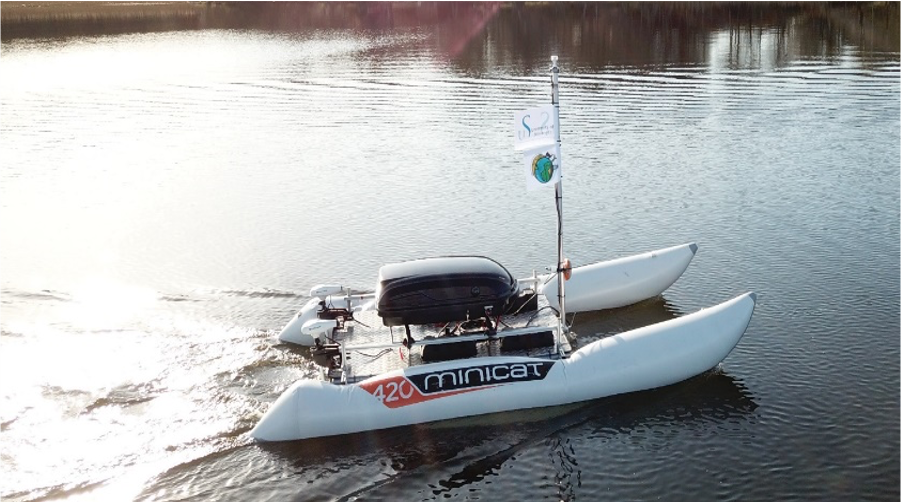
Wiktor Weibull and Thomas Meldahl Olsen from UiS in collaboration with Maritime museum, Archeological Museum, GeoPluss aims to develop methods to efficiently collect, process and interpret 2D and 3D near surface geophysical data. It will take in use autonomous vehicles and fast and repeatable geophysical sources to produce dense coverage of the near subsurface. It will also investigate geostatistical methods to optimally interpolate the scattered data into regularly and densely sampled 3D models. As a part of the project, the models and data will be tied to geotechnical and archeological data and interpreted using methodologies borrowed from the E&P industry.
Large Autonomous Subsea Freight-Glider
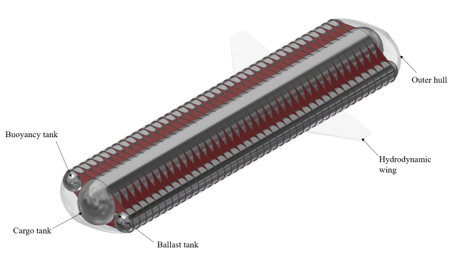
In this research work, a novel subsea freight-glider system is proposed as a suitable, cost-effective, energy-efficient alternative to tanker ships and pipelines. The proposed vehicle is autonomous, 50 m long, has a 1500 DWT displacement, and can carry approximately 800 tons of cargo. The subsea freight-glider uses variable-buoyancy propulsion instead of traditional propellers/thrusters. It changes ballast to provide positive/negative net buoyancy allowing it to glide subsea through the water using hydrodynamic wings. This is an extremely energy-efficient way of transporting large amounts of cargo over medium/long distances. Since the freight-glider operates subsea, it is not affected by wind and waves and can operate in any weather condition. Furthermore, subsea fields that are not large enough to justify the installation of subsea pipelines can still be developed. The subsea freight-glider is proposed as a vehicle for liquid cargo transport such as CO2, hydrocarbons, injection fluids and gasses. It can also be configured to carry solid cargo and even electrical power using batteries. Professor Yihan Xing is leading this research work at UiS.
DigiFloDock Project

The University of Stavanger, CoreMarine, Mykelbust Verft in Norway together with the Project promoter Gdańsk University of Technology in Poland – received funding for the project “A Floating Dock Digital Twin towards Efficient, Safer and Autonomous Docking Operations”, a project which aims to improve the automation, efficiency and safety of the floating docking operations by developing a digital twin solution, which can predict, identify and prevent dangerous situations during an autonomous docking process.
University of Stavanger will be responsible for numerical simulation procedures. They bring their knowledge and experience in kinematics and dynamics of floating docks and vessels. They will also share their expertise in strength and stability calculations.
Professor Muk Chen Ong, Professor II Lin Li, PhD Jianan Zhang and Postdoc Xueliang Wen are the contact persons from UiS. The project started 1 Feb 2021, 36 months in total.
OFFSHORE Project
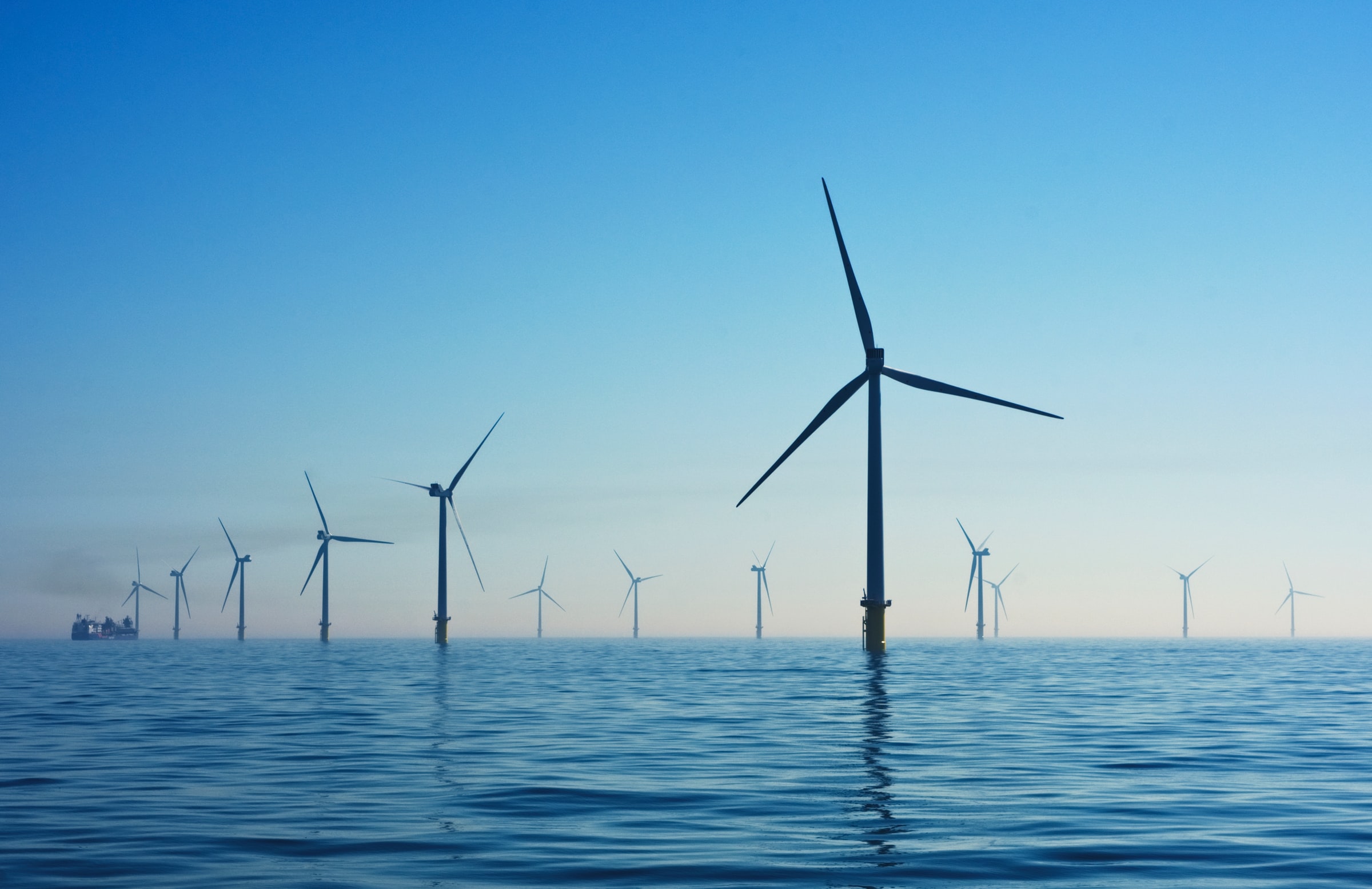
UiS researchers got funding for Polish-Norwegian collaboration for 3 million. Professor Muk Chen Ong and researcher Marek Janocha at the Department of Mechanical and Structural Engineering and Materials Science at UiS have received funding for a Polish-Norwegian project aimed at developing bilateral research collaboration.
The project lasts one year, until March 2024.
The Clean Arctic Shipping Initiative
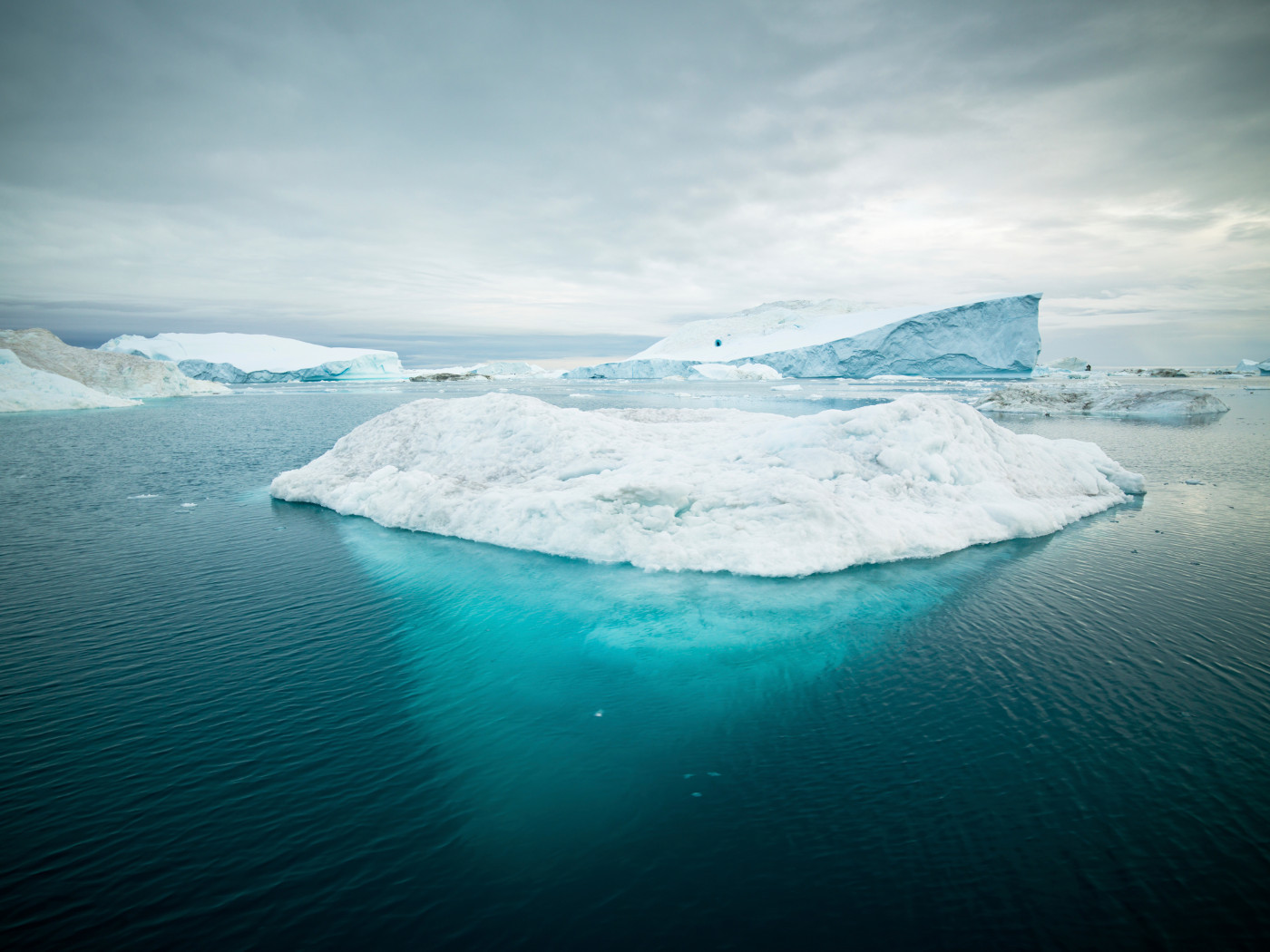
The goal is to find environmentally friendly solutions for shipping and transport in Arctic waters.